In the first part of this article, we discussed the major challenges that manufacturing companies face. The solution to these challenges lies in implementing SCADA and MES systems. These systems enable transparent management and optimization of production processes. While SCADA focuses on monitoring and controlling production equipment, MES is dedicated to production management, planning, tracking efficiency, and ensuring smooth production operations.
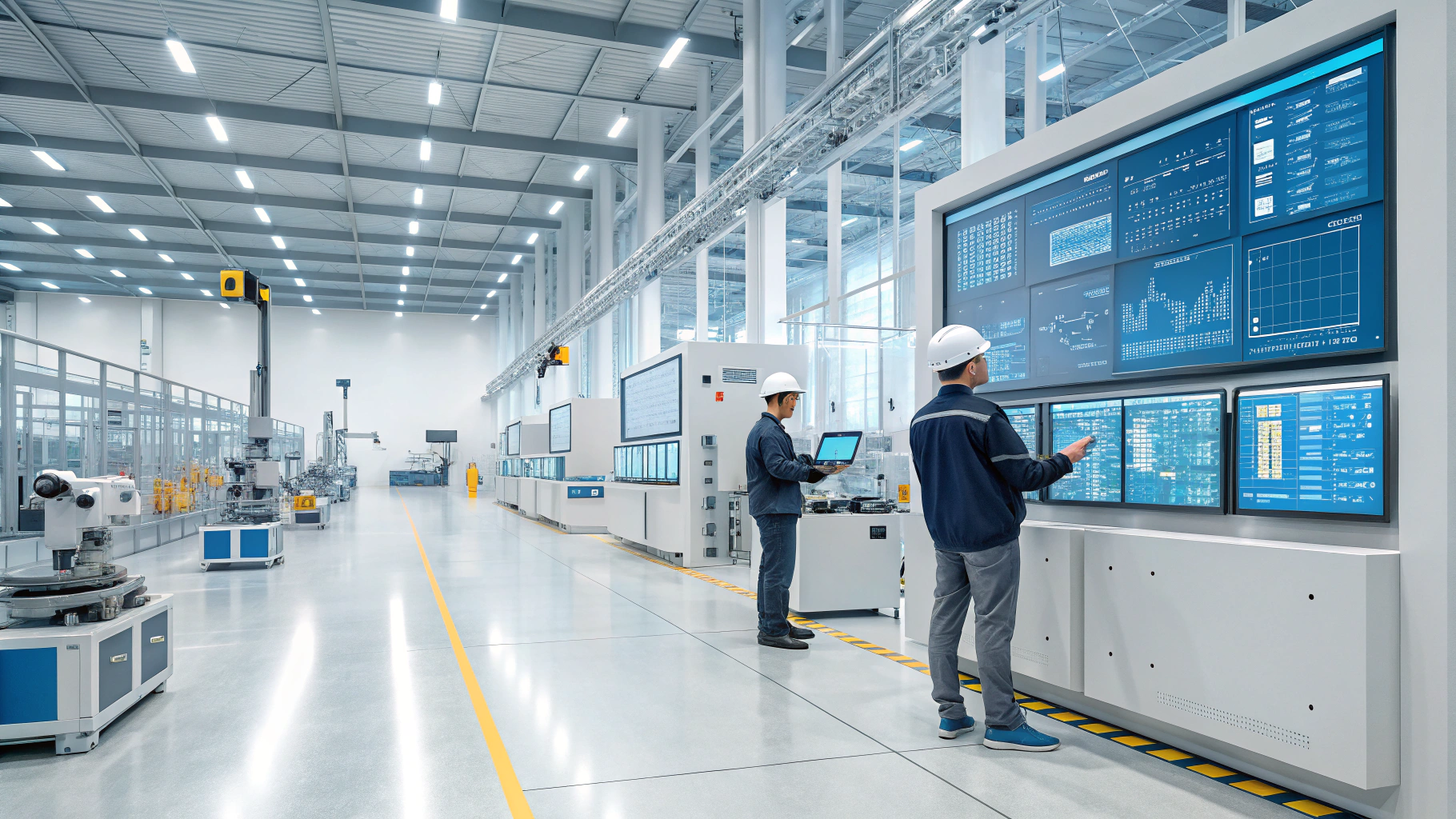
➡️ SCADA
SCADA (Supervisory Control and Data Acquisition) serves as the eyes and hands of operators. It provides real-time oversight of manufacturing technology. It primarily communicates with PLC (Programmable Logic Controller) systems, which control individual machines. However, in the IoT environment, SCADA can also communicate directly with sensors via protocols such as MQTT and OPC UA.
✅ Immediate Response to Failures
One of the key advantages of SCADA is its ability to immediately respond to failures, minimizing downtime and reducing production losses. If a machine shuts down unexpectedly, experiences performance drops, or technological deviations (e.g., unacceptable temperatures or pressures), operators can quickly intervene and restore production.
✅ Remote Control of Technology
Another key feature of SCADA is remote control of technology. It allows operators to turn equipment on and off remotely, as well as adjust parameters such as speed, pressure, and temperature directly from their interface without having to be physically present at the machine.
✅ Historical Data Storage for Analysis and Optimization
SCADA also stores historical data, enabling not only retrospective analysis of problems but also long-term improvements in production processes.
❓ When is SCADA (Not) Suitable for a Business?
If a SCADA system were not implemented, operators in smaller plants might be able to manage oversight manually. However, in large-scale enterprises, this would significantly extend response times and cause losses. Additionally, without data collection, it would be impossible to generate accurate reports, further complicating strategic decision-making at the management level.
➡️ MES
While SCADA monitors technological equipment, MES (Manufacturing Execution System) manages the production process itself. It integrates machines, materials, and workers to provide a comprehensive view of the entire production process — from planning and execution to storage. While SCADA collects data at intervals of seconds, MES links them to orders, allowing managers to monitor production status in real-time and respond to deviations immediately.
✅ Digitalization and a Unified Data Source
The MES system replaces paper-based processes with electronic data collection, ensuring that all information is available in real-time and eliminating errors caused by manual data handling.
It allows both automated and manual data entry throughout the entire production process, creating a single source of truth (SSOT). All data is centrally recorded and accessible at every level of management, eliminating delays, inaccuracies, and adjustments caused by manual reporting. Decision-making is based on hard real-time data.
✅ Automated Production Planning
One of the main benefits of MES is automated production planning. The system uses data from ERP (e.g., SAP) to manage manufacturing operations based on orders and available resources, providing a complete real-time overview of production status (WIP – Work in Progress). MES also synchronizes production data with ERP systems, ensuring seamless data exchange between the company and the shop floor without the need for manual intervention.
✅ Efficient Workforce Management
The system ensures that only qualified employees are assigned to production operations. By logging into the MES system, employees verify their credentials, and the system checks whether they meet the requirements for operating a specific machine or performing a particular task. This process eliminates errors caused by unqualified workers and reduces the likelihood of workplace accidents.
✅ Optimization of Resource Utilization
MES provides detailed insights into the use of production resources, whether it be machines, materials, or personnel. It monitors equipment conditions, reports failures, and alerts to potential shortages of materials. If necessary, the system automatically notifies the warehouse to replenish materials before production is disrupted. This approach minimizes downtime and maximizes resource utilization.
✅ Production and Product Traceability
Every manufactured unit or batch is linked to all production data — from raw materials and individual operations to the final product. This system allows for full traceability in the event of a complaint, which is crucial in industries with strict regulations, such as pharmaceuticals and food production.
✅ Quality and Performance Management
MES actively monitors the quality of production processes. It detects deviations from standards and immediately signals them, minimizing the risk of production errors. Quality data can be integrated with external software for Statistical Process Control (SPC) or Laboratory Management Systems (LMS), ensuring even more precise quality management.
The system also calculates OEE (Overall Equipment Effectiveness), identifying production bottlenecks and providing tools for their optimization.
✅ Digitalization of Documentation
MES automates document management, ensuring that workers have access to all necessary information, such as work instructions, technical drawings, and safety guidelines, at the right time. Documentation is available electronically, often via QR codes placed directly on machines, reducing the need for physical documents and increasing operational efficiency.
✅ Efficient Maintenance Management
MES plays a significant role in maintenance management. The system enables preventive maintenance planning, reducing unexpected failures and minimizing costs associated with reactive maintenance. Maintenance staff can log interventions, plan tasks, and monitor equipment status directly in the system.
MES also analyzes historical equipment performance data, allowing businesses to predict potential failures before they occur. In combination with SCADA, businesses can gradually transition to predictive maintenance, leveraging advanced analytical algorithms to detect anomalies and prevent failures before they happen.
❓ When is MES (Not) Suitable for a Business?
Not every business requires all MES system functionalities. While some companies implement only selected modules to address specific issues, industries such as pharmaceuticals or food production (F&B) often require a comprehensive MES system. These sectors must ensure batch traceability, quality control, and strict regulatory compliance, as even the smallest mistake can have serious consequences for consumer health.
Companies that aim to improve efficiency, reduce costs, and increase competitiveness can no longer rely on outdated manual processes and paper-based records. SCADA and MES are not just technologies—they are strategic tools that enable businesses to transition to smart manufacturing, driven by real-time data and automated processes. Are you ready to take the next step?
10 Reasons to Implement SCADA and MES
📌 1. Increased transparency in production processes
📌 2. Faster and more accurate reporting
📌 3. Precise inventory management
📌 4. Immediate response to issues
📌 5. Reduced downtime and prevention of unplanned failures
📌 6. Improved workforce management and error reduction
📌 7. Higher product quality and elimination of production defects
📌 8. Complete traceability and tracking of production processes
📌 9. Increased efficiency, productivity, and optimization of production resources and costs
📌 10. Readiness for Industry 4.0 and future innovations
Why Choose IoT/IIoT Implementation with IoT Industries?
Traditional companies typically specialize in OT (operational technologies, such as production lines and devices) or classic enterprise IT systems. However, we are able to connect both of these worlds. Our unique expertise in integrating OT and IT allows us to deliver innovative solutions in digital transformation, enhancing efficiency, reliability, and competitiveness for manufacturing companies.