Výroba sa dnes mení rýchlejšie ako kedykoľvek predtým. Globalizovaný trh, kolísavý dopyt, rastúce náklady, čoraz vyššie nároky na dodacie lehoty a flexibilitu. To všetko vedie k tomu, že už nestačí iba vyrábať. Treba vyrábať efektívne. Každý zbytočný krok, každý nevyužitý zdroj, každá nepresnosť v plánovaní či údržbe predstavuje stratu času, peňazí, zdrojov, reputácie a v konečnom dôsledku i konkurencieschopnosti.
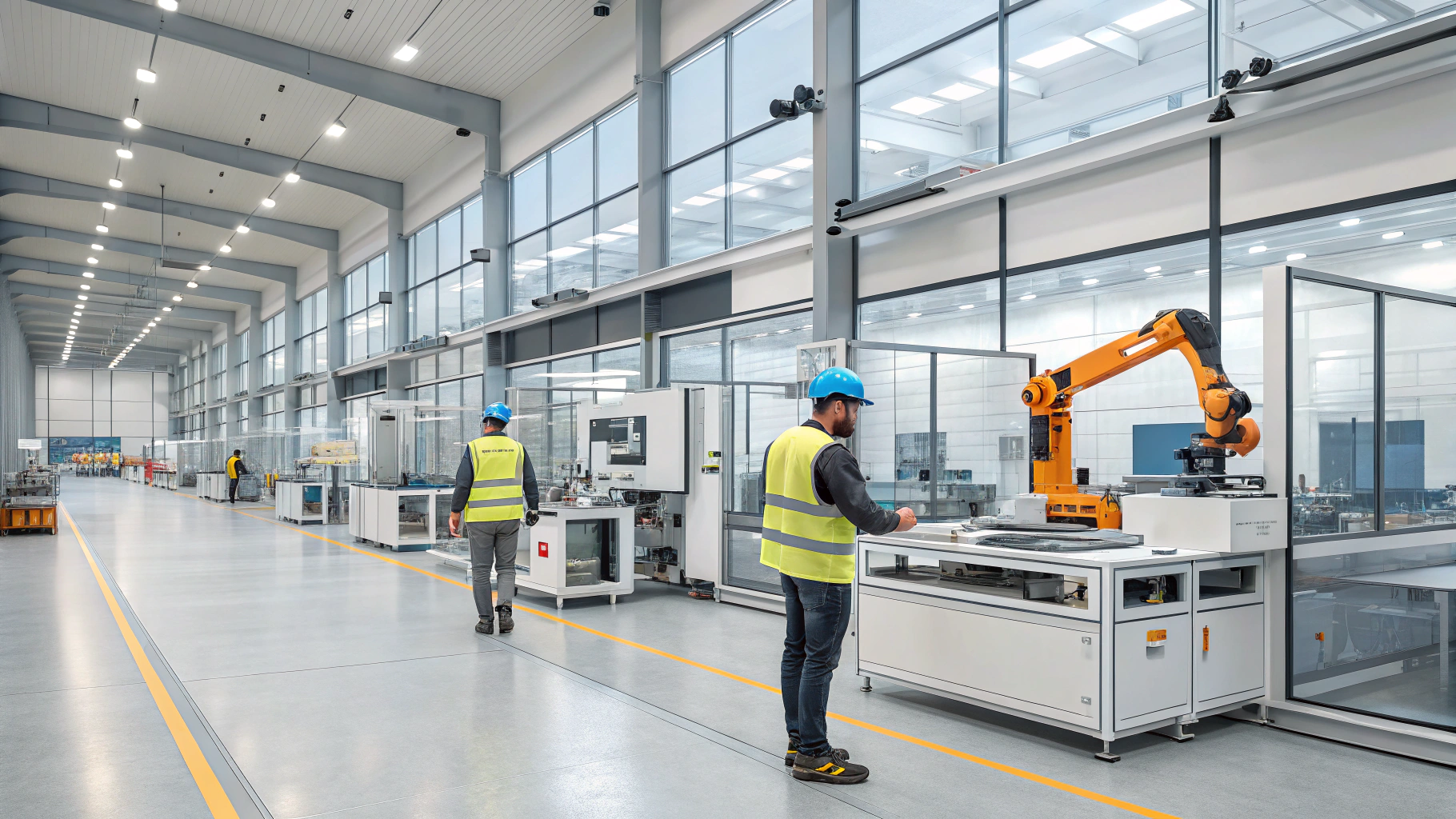
Čo je teda tým pomyselným kľúčom k udržateľnej efektivite? Nie je to zvyšovanie výkonu ľudí, ani nakupovanie nových technológií bez jasnej stratégie. Kľúčom je optimalizácia výrobných procesov. Nejde však o jednorazový projekt, ale o systematický prístup, ktorý neustále hľadá úzke miesta, odhaľuje skryté rezervy a premieňa dáta na konkrétne zlepšenia v reálnom čase. A tak prináša nižšie náklady, vyššiu produktivitu a celkovo lepšiu výkonnosť podniku.
Prečo optimalizácia výrobných procesov často zlyháva?
Mnohé firmy už opakovane skúšali „zefektívniť“ výrobu. Zmodernizovali stroje, upravili zmeny, zaviedli KPI… No aj napriek tomu sa problémy stále opakujú. Výroba mešká, náklady rastú, konkurencieschopnosť klesá. Dôvod? Bez spoľahlivých dát nie je možné objektívne identifikovať, kde presne problémy vznikajú, čo ich spôsobuje a ako ich odstrániť. A optimalizácia výrobných procesov tak obvykle skončí pri symptómoch, nie pri príčine.
Tým sa dostávame k najčastejšiemu dôvodu, prečo optimalizácia zlyhá. Veľa výrobných firiem totiž stále pracuje s nepresnými alebo neúplnými údajmi. Zber dát prebieha manuálne, reporty prichádzajú oneskorene a často si odporujú. V konečnom dôsledku sa tak rozhodnutia zakladajú na odhadoch, intuícii alebo historických šablónach, nie na aktuálnej realite. A bez reálnych dát nie je možná ani reálna optimalizácia výroby.
Ako by mala vyzerať skutočne efektívna optimalizácia výroby?
Optimalizácia výrobných procesov neznamená len urobiť niečo rýchlejšie či lacnejšie. V skutočnosti ide o oveľa systematickejší a strategickejší prístup. Znamená to pochopiť celý hodnotový tok. Od momentu, keď materiál vstúpi do podniku, cez každý krok jeho spracovania, až po finálnu expedíciu hotového výrobku. Cieľom je identifikovať a eliminovať všetko, čo neprináša zákazníkovi hodnotu. V praxi to znamená niekoľko zásadných krokov:
✅ Získať úplný a transparentný prehľad o stave výroby v reálnom čase. Pretože len ak máte k dispozícii aktuálne a presné dáta, dokážete identifikovať úzke hrdlá a prijímať rozhodnutia na základe reality, nie domnienok.
✅ Minimalizovať plytvanie vo všetkých formách. Či už ide o plytvanie časom, materiálom, strojmi, ľudským kapitálom alebo energiami. Každý z týchto typov plytvania znamená nevyužitý potenciál a zbytočné náklady.
✅ Zefektívniť plánovanie a riadenie výroby. Namiesto plánovania na základe ideálnych modelov alebo historických šablón, je nevyhnutné plánovať na základe aktuálnych priorít a reálnej kapacity, ktorá zahŕňa dostupnosť pracovníkov, strojov, materiálov.
✅ Zmeniť prístup k údržbe z reaktívneho na plánovaný a podmienený. To znamená, že namiesto riešenia porúch až po ich vzniku, podnik pracuje s dátami o aktuálnom technickom stave strojov a ich výkonnosti.
Akú rolu v tom zohráva digitálna transformácia?
Vďaka digitálnej transformácii zber dát neprebieha ručne, ale automaticky priamo zo strojov, výrobných liniek, senzorov a meracích zariadení. Tieto informácie sa okamžite prepájajú s ďalšími systémami, ako sú ERP, skladové systémy, systémy údržby alebo kontroly kvality. Výsledkom je jednotný a konzistentný zdroj pravdy (SSOT – Single Source of Truth), na ktorý sa môže spoľahnúť každá úroveň riadenia, od operátora až po generálneho riaditeľa.
Aby však takéto komplexné dátové toky mohli fungovať ako jeden súvislý celok, je nevyhnutné nasadiť správne nástroje. Práve tu vstupujú do hry moderné digitálne riešenia ako SCADA, MES či EMS, ktoré spoločne vytvárajú prepojený a centralizovaný ekosystém. Ten umožňuje firmám zhromažďovať, analyzovať a vizualizovať všetky dáta naprieč celou výrobou. V reálnom čase a z jedného miesta.
Výhodou tohto prístupu je, že dáta nie sú „ukryté“ v zložitých tabuľkách, ale sú prehľadne spracované do interaktívnych dashboardov, ktoré okamžite poskytujú jasný pohľad na dostupnosť materiálov, stav zariadení, spotrebu energií, stav výroby či odchýlky od plánu. Už nie je potrebné čakať na týždenné reporty alebo ručne zhromažďovať informácie z rôznych oddelení. Všetko je dostupné ihneď, na jednom mieste.
V prípade poklesu efektivity, výpadku zariadenia či iných anomálií dokáže vedenie firmy zareagovať okamžite. Optimalizácia výrobných procesov sa tak stáva proaktívnym nástrojom riadenia, nie len reaktívnym vyhodnocovaním minulosti. Namiesto hasenia problémov im firmy dokážu predchádzať. A čo je ešte dôležitejšie, optimalizácia výroby sa tak mení z jednorazovej aktivity na nepretržitý, dátami riadený proces zlepšovania.
Komplexné riešenie na mieru od IoT Industries
V IoT Industries veríme, že skutočná optimalizácia výrobného procesu začína presnými dátami a správne prepojenými systémami. Pomáhame výrobným podnikom nastaviť celý dátový tok, od zberu až po vizualizáciu, tak, aby sa mohli rozhodovať efektívnejšie, rýchlejšie a s väčšou istotou. Ak chcete vedieť, kde vo vašej výrobe vznikajú zbytočné náklady a ako ich premeniť na úspory a výkonnosť, radi vám ukážeme, ako na to. Neváhajte nás kontaktovať.
Prečo sa rozhodnúť pre implementáciu IoT/IIoT práve s IoT Industries?
Tradičné firmy sa spravidla špecializujú na OT (operačné technológie, ako sú výrobné linky a zariadenia) alebo klasické podnikové IT systémy. My však dokážeme oba tieto svety prepojiť. Naša unikátna expertíza v prepájaní OT a IT nám tak umožňuje prinášať klientom inovatívne riešenia v oblasti digitálnej transformácie, ktoré zvyšujú efektivitu, spoľahlivosť a konkurencieschopnosť výrobných podnikov.